Technology
Green electrometallurgy
Country
Ukraine
Application in details
The process of smelting steel using electricity.
In 2012, the open-hearth shops for metal smelting were closed here and the process of steel smelting using electricity was launched. This allowed to reduce gas consumption by eight times. If the open-hearth shop consumed about 145 cubic meters of gas to smelt a ton of steel, then after the launch of the new plant, this figure fell to 18 cubic meters.
The closure of dirty production allowed to reduce CO2 emissions tenfold. Now the emission level for smelting a ton of steel is less than 250 kg. The level of CO2 emissions at the new electric arc furnace complex «Interpipe Steel» is even lower than the norm that the EU plans to achieve by 2050.
Scalability
The electric steel-smelting complex produces the maximum volume of products during the hours when electricity consumption in the power system is minimal, i.e. at night. On a national scale, this allows the most efficient consumption of electricity from nuclear power plants at the time when it is least in demand for household and other consumers.
Current application sites/areas
Interpipe Steel electric steel plant in Dnipro, Ukraine
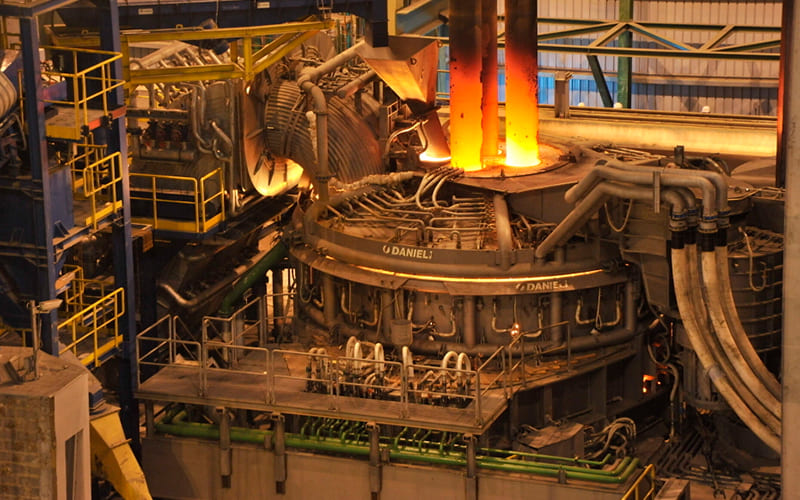